Case studies: A plant that specializes in the drying of softwood
Significant improvement in production
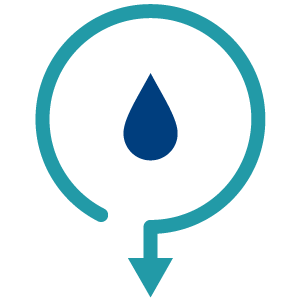
-80%
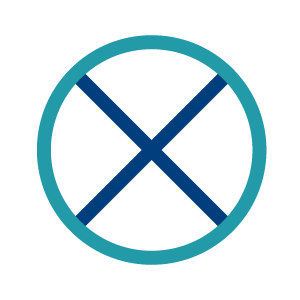
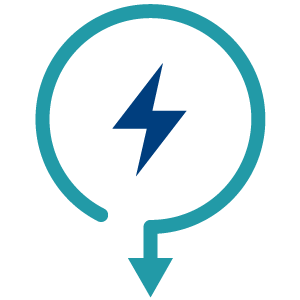
-1 000 000
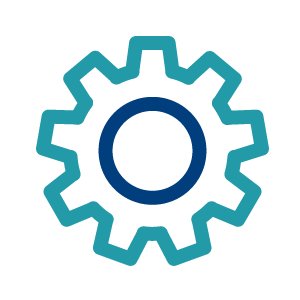
Context
Operating a steam boiler in the wood drying industry presents several challenges. Sudden and sustained steam demands promote water carryover, which significantly reduces drying performance due to the loss of steam's energy content. This not only lowers the process efficiency but also causes erratic boiler operation due to water level fluctuations, piping "washout" issues, hot water loss, and difficult control of the treatment program.
At this drying plant, there were few alternatives other than lowering the boiler water conductivity to reduce as much as possible the water carryover phenomenon. This measure, already very inefficient, involved increasing the blowdown rate and consequently, a costly loss of energy and treated water.
Solution
The conductivity maintained in boiler water is related to the concentration cycles achieved before blowdowns are performed. These blowdowns aim to remove dissolved solids accumulated in the water, which can promote water carryover into the steam. These solids come from makeup water and the treatment products added to protect equipment against corrosion and scaling. Typically, these products are mineral-based and directly contribute to water conductivity.
The Aquafilm V program was implemented as a replacement for conventional treatment, aiming to control water carryover issues while minimizing blowdown rates. This recommendation is based on the low contribution of the Aquafilm program to boiler water conductivity since the treatment relies on the use of volatile organic ingredients.
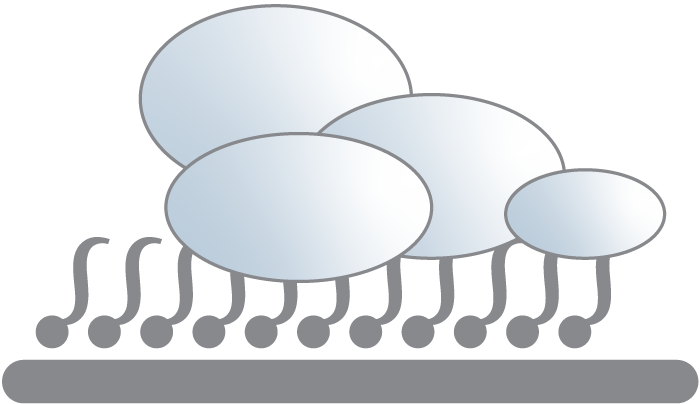
Aquafilm V forms a protective film on metal
During the period evaluated with conventional treatment (Phase 1), water carryover was excessively high with peaks exceeding 3000 μmhos/cm in the condensate. Even by significantly increasing the blowdown rate (Phase 2), demonstrated by the drop in chloride concentration in the boiler water, episodic spikes in condensate conductivity were still observed. From the moment the Aquafilm V program was implemented (Phase 3), condensate conductivity dropped and stabilized at an average of 9 μmhos/cm. The subsequent gradual increase in concentration cycles had no impact on steam quality.
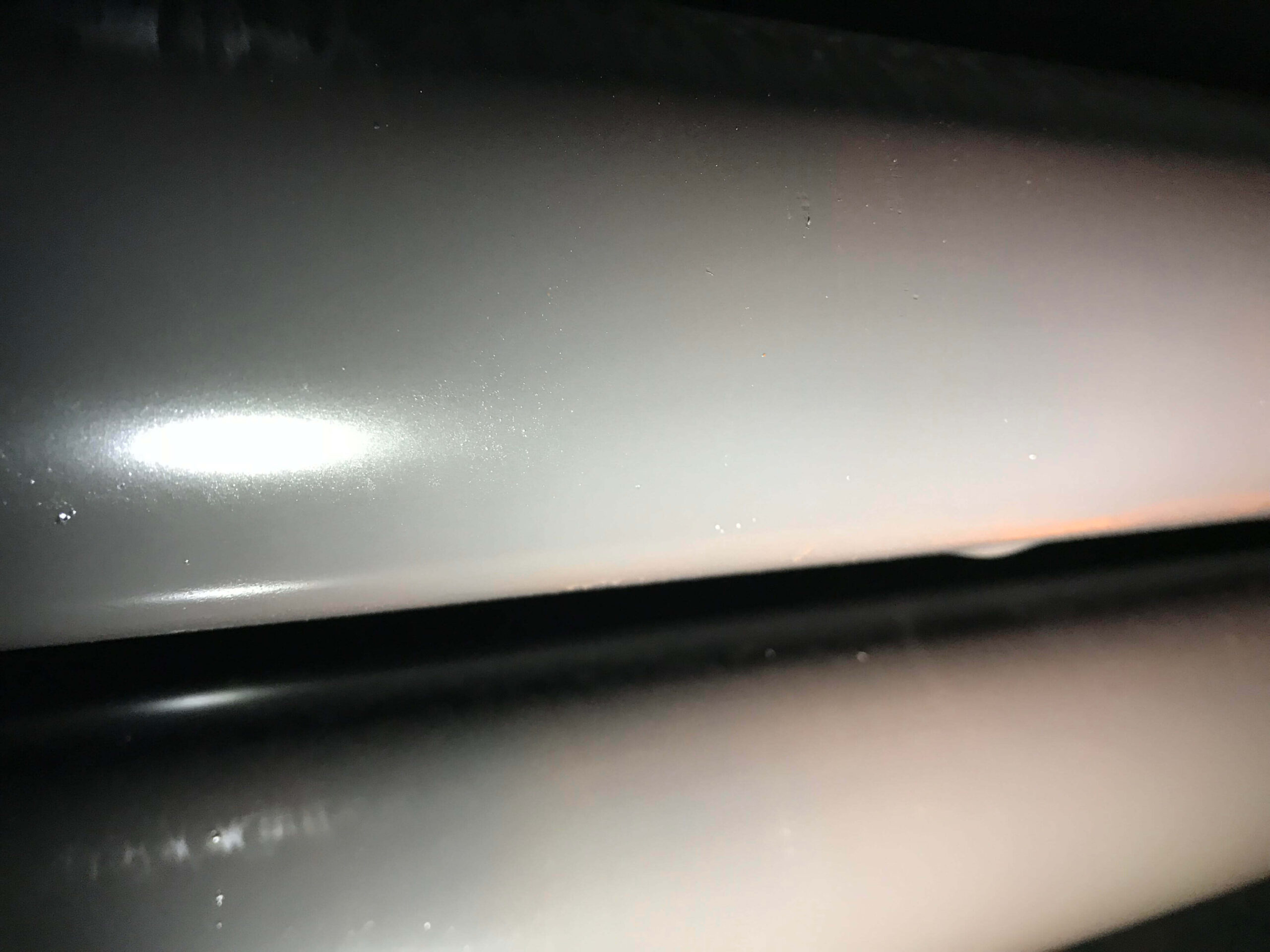
Aquafilm V
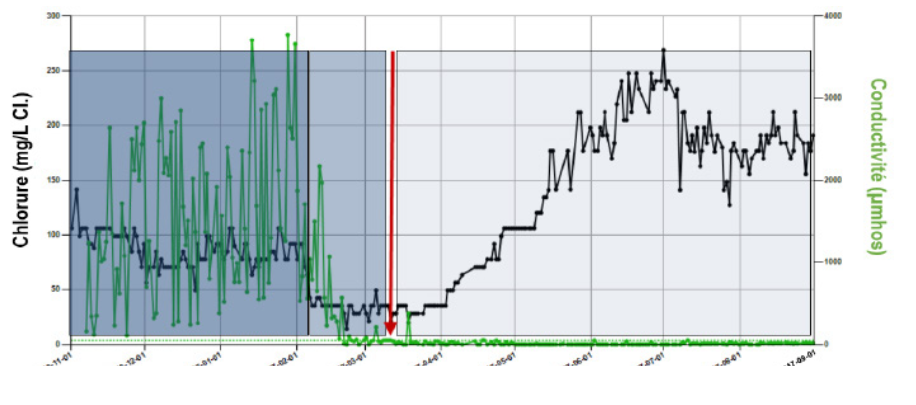
Conclusion
Introducing Aquafilm technology has solved the recurring problem of water carry-over in steam, which had a drastic effect on the efficiency of the drying process. The use of volatile organic ingredients is clearly more advantageous than other conventional methods. Aquafilm improves the efficiency of operations, reduces blowdown rates, increases energy savings, and promotes treatment program stability.
Stop wasting time and money on bottlenecks
caused by entirely avoidable downtime!