ENHANCED PRODUCTION achieved through improved dryer feed.
Case Study : Wood Processing Plant
Case Study : Wood Processing Plant
Significant reduction in boiler blowdown
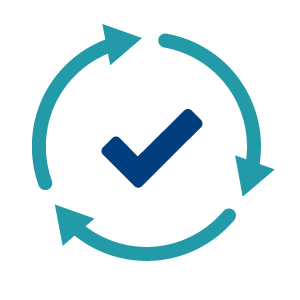
Major increase in cycles of concentration
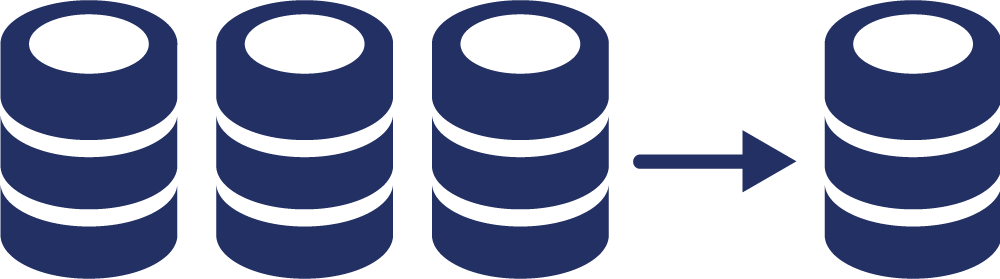
Decrease in number of products
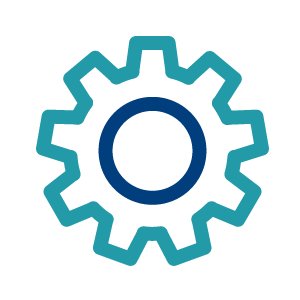
Overall process improvements
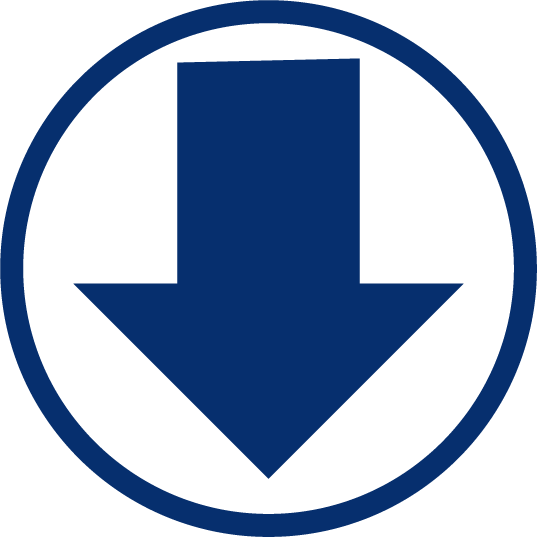
14% reduced gas consumption and CO₂ emissions
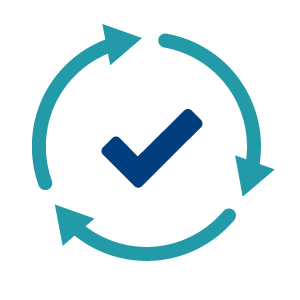
Major increase in cycles of concentration
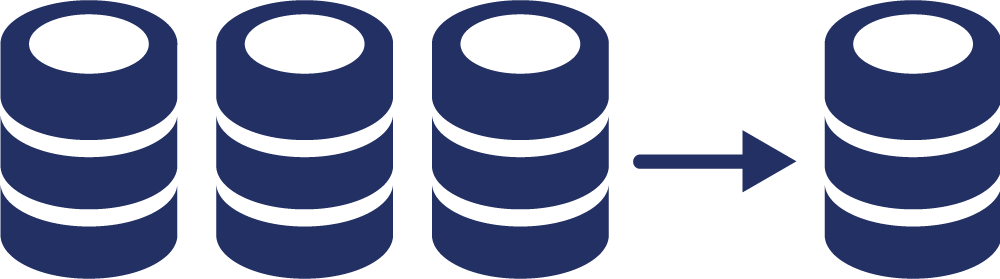
Decrease in number of products
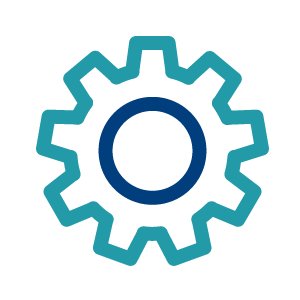
Overall process improvements
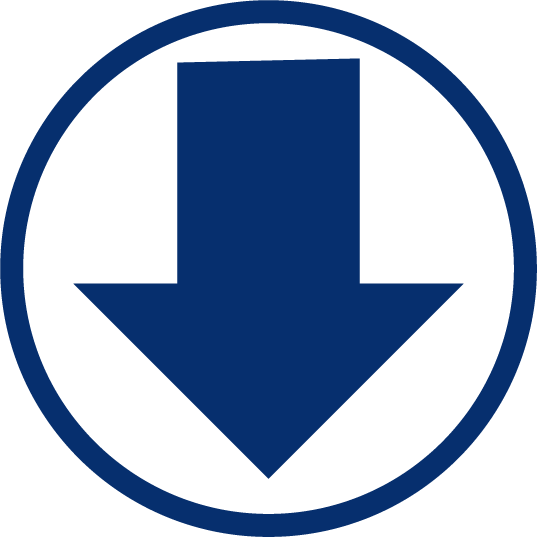
14% reduced gas consumption and CO₂ emissions
CHALLenGE
Over the next six years, Canada’s carbon pricing is set to nearly triple the mill’s base fuel cost per GJ, while usa mills will not experience an increase. To ensure the client remains competitive, they wanted
to improve steam boiler efficiencies to reduce expenses. The mill utilizes two steam boilers and one hot water boiler to heat wood drying kilns.
‘’ With the increased operating efficiencies at our boilers, we essentially dried more lumber, while burning less gas, while creating less CO₂ emissions. Results that can’t be argued! These results didn’t all happen on their own.‘’
- Brad Mason, General Manager of Manifacturing,
Kalesnikoff Lumber
Solution
Magnus’ steam boiler audit revealed that increased efficiencies would result in substantial savings and improved boiler operation. Aquafilm V technology was implemented at the beginning of 2023 replacing the outgoing conventional chemical treatment program.
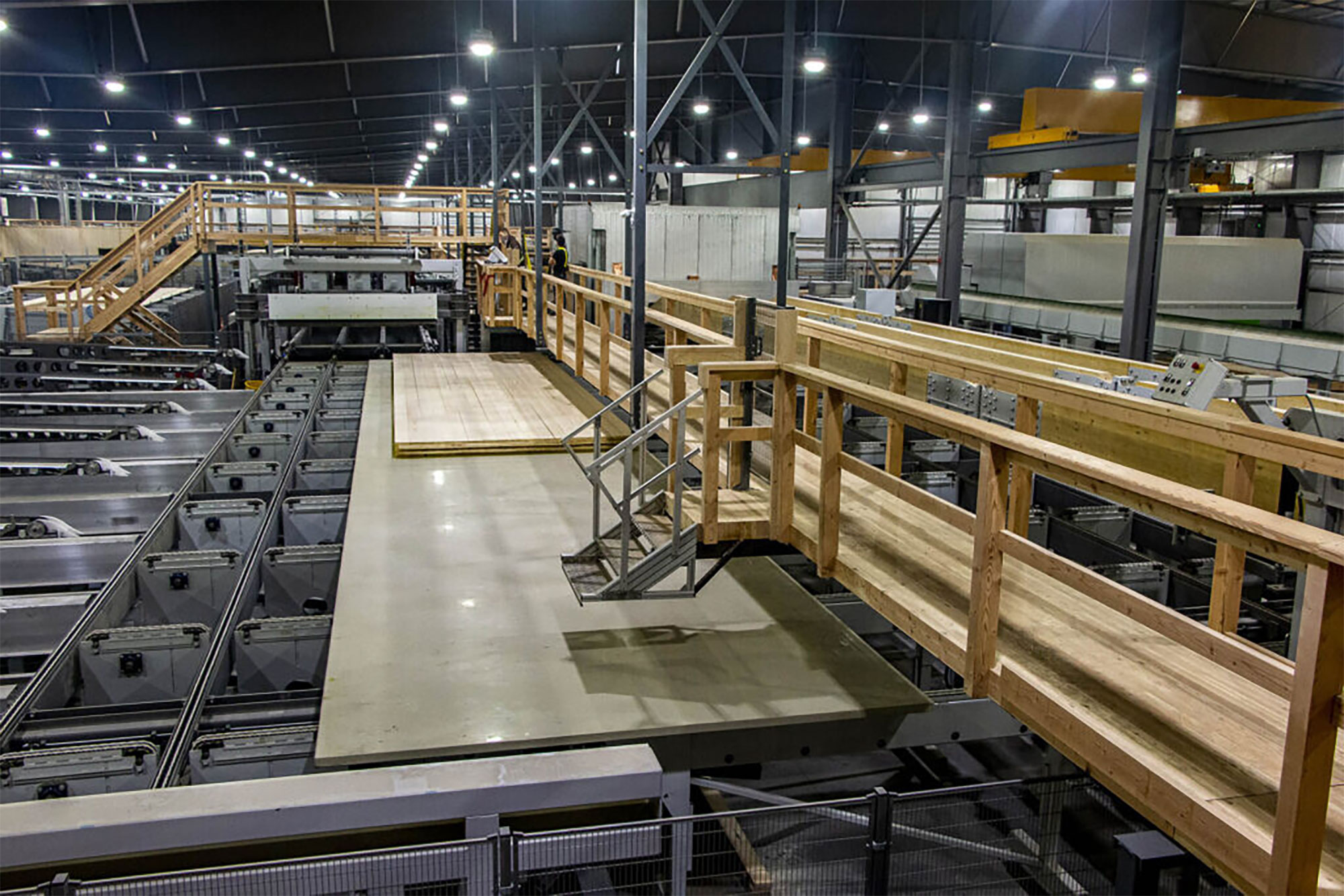
resuLts
Within weeks of implementing Aquafilm V, system performance improved. There were reductions of dissolved iron levels throughout the steam network, indicating reduced corrosion. In addition, the boilers were able to run higher cycles, with less boiler water carry-over. The mill was able to run more kiln hours than the previous year while using less gas. Based on 12 months of operation, data showed more than a 14% reduction of natural gas consumption and CO₂ emissions.
Stop wasting time and resources:
reduce your chemical consumption!