FOR A REDUCTION OF THE CARBON FOOTPRINT
Case study: cardboard packaging company
Stop wasting water with conventional treatments.
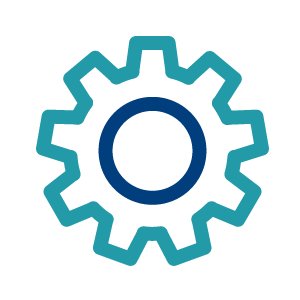
Overall process
improvements
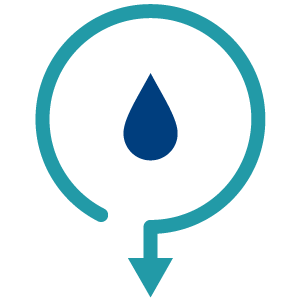
26%
reduced
water use
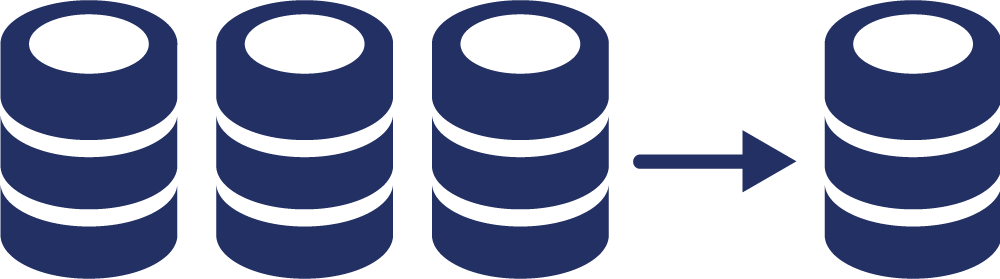
Decrease in number
of products
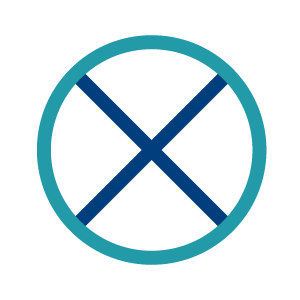
Eliminated two pumps/injection points
CHALLENGE
A Wisconsin based corrugated packaging facility was experiencing increased demands on time required for their maintenance team to manage their boiler water treatment program. They were also looking for ways to improve safety surrounding chemical handling for products that were required for their program.
Solution
It was recommended to switch to Aquafilm V, a one drum organic product.
Although the switch in product was made to reduce program management time and improve
safety, it resulted in additional benefits, including fantastic water savings.
The chart below demonstrates the results achieved by switching to Aquafilm V.
Average Feedwater Conductivity
Boiler Cycles of Concentration
Year 1
214.4
11.9
Year 2
134.5
17.9
BENEFIT
-37%
+34%
RESULTS
- Annual makeup water use decreased, resulting in 26% water savings.
- Simplified program – switched from three treatment chemicals to one.
- Reduced chemical program management time for onsite personnel.
- Eliminated two pumps/injection points reducing maintenance & potential leak points.
- Improved safety with use of organic chemistry.
- Cut boiler testing time in half for the customer, saving them 65 hours annually.