
Reduction of
energy consumption

Reduction of
GHG Emissions

Reduction of
Water Consumption

Safer for
the operator
REDUCE YOUR ENVIRONMENTAL FOOTPRINT AND CUT COSTS
Reduces product shipping, handling and testing by up to 80%
REDUCE YOUR ENVIRONMENTAL FOOTPRINT AND CUT COSTS
Reduces product shipping, handling and testing by up to 80%
Aquafilm V for Steam BoilersAquafilm V is a revolutionary eco-friendly boiler water treatment technology based on the formation of a protective film on surfaces for the treatment of steam boilers.
This technology makes it possible to protect the entire network, from the feed to the condensate return, with a single product.
Learn More
Aquafilm V is a revolutionary eco-friendly boiler water treatment technology based on the formation of a protective film on surfaces for the treatment of steam boilers.
This technology makes it possible to protect the entire network, from the feed to the condensate return, with a single product.
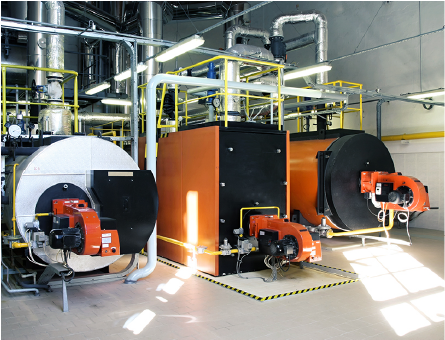
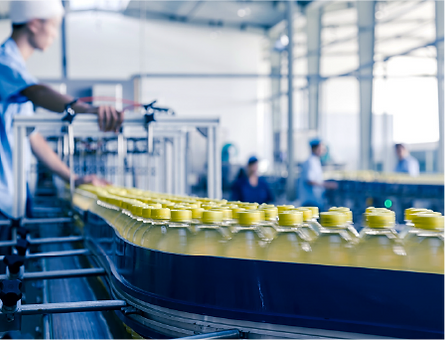
Aquafilm V for Steam Boilers with Food Contact
Aquafilm V is an all-in-one, all-organic product and FDA CFR 173.310 compliant for food plants.
Aquafilm V can replace multiple chemicals which are used for the conventional treatment of steam boiler systems.
Learn More
Aquafilm V for Steam Boilers with Food Contact
Aquafilm V is an all-in-one, all-organic product and FDA CFR 173.310 compliant for food plants.
Aquafilm V can replace multiple chemicals which are used for the conventional treatment of steam boiler systems.
A REVOLUTIONARY TECHNOLOGY WITH FILM FORMING AGENTS FOR STEAM BOILERS
Aquafilm V protects your boilers’ integrity & steam quality while enhancing your system’s life and reliability.
In fact, whenever you choose Aquafilm V, you can be certain that you’re getting one of the safest and most innovative eco-friendly boiler water treatment solutions.
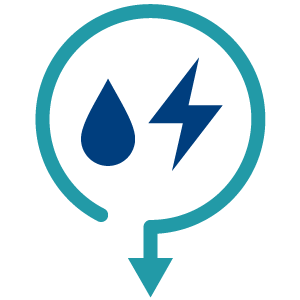
- The all-organic formula improves condensate quality.
- Saves money by reducing blowdowns.
- Reduces makeup water and chemicals required.
- Lowers energy costs by improving heat transfer inside the boiler.
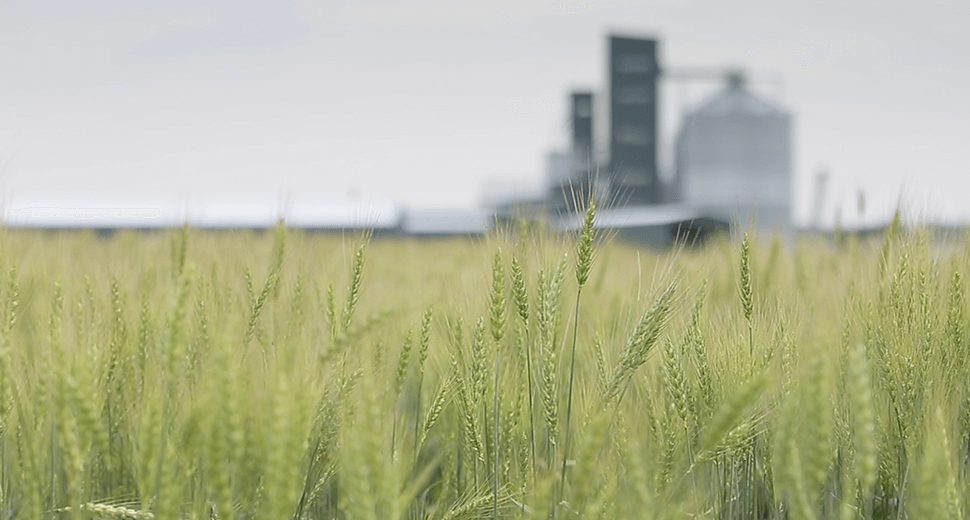
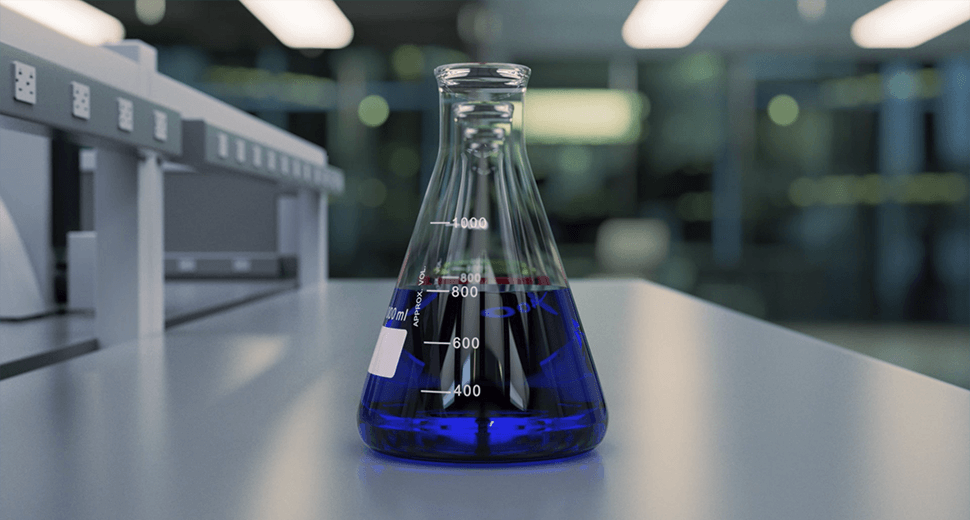
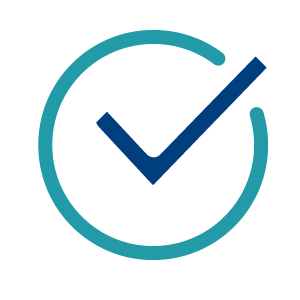
- Significantly reduced health and safety risks.
- Eliminates chemical handling by up to 80%.
- Simplified dosing.
- Reduced testing requirements.
- Reduced CO2 emissions.
- Readily biodegradable.
- In accordance with FDA guidelines and complies with OECD 301 A-F criteria.
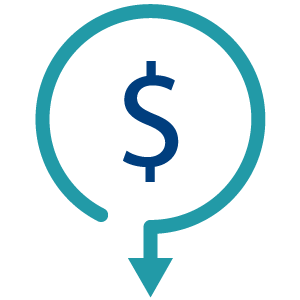
- Reduces boiler carryover to ensure higher quality steam.
- Improves system reliability and lifespan.
- Reduced maintenance costs from lower corrosion and scaling.
- Protects feed-tanks, boilers, steam pipes, turbines, and condensate lines.
- Gradually dislodges existing scale, prevents the formation of new deposits, and improves the condition of the system’s internal surfaces.
- Simplified water testing.
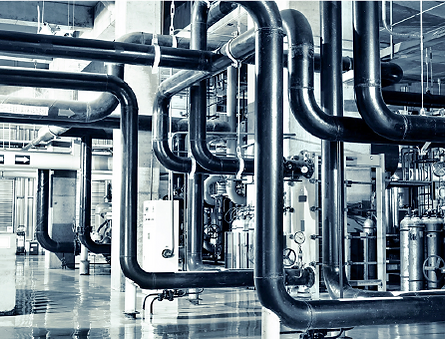
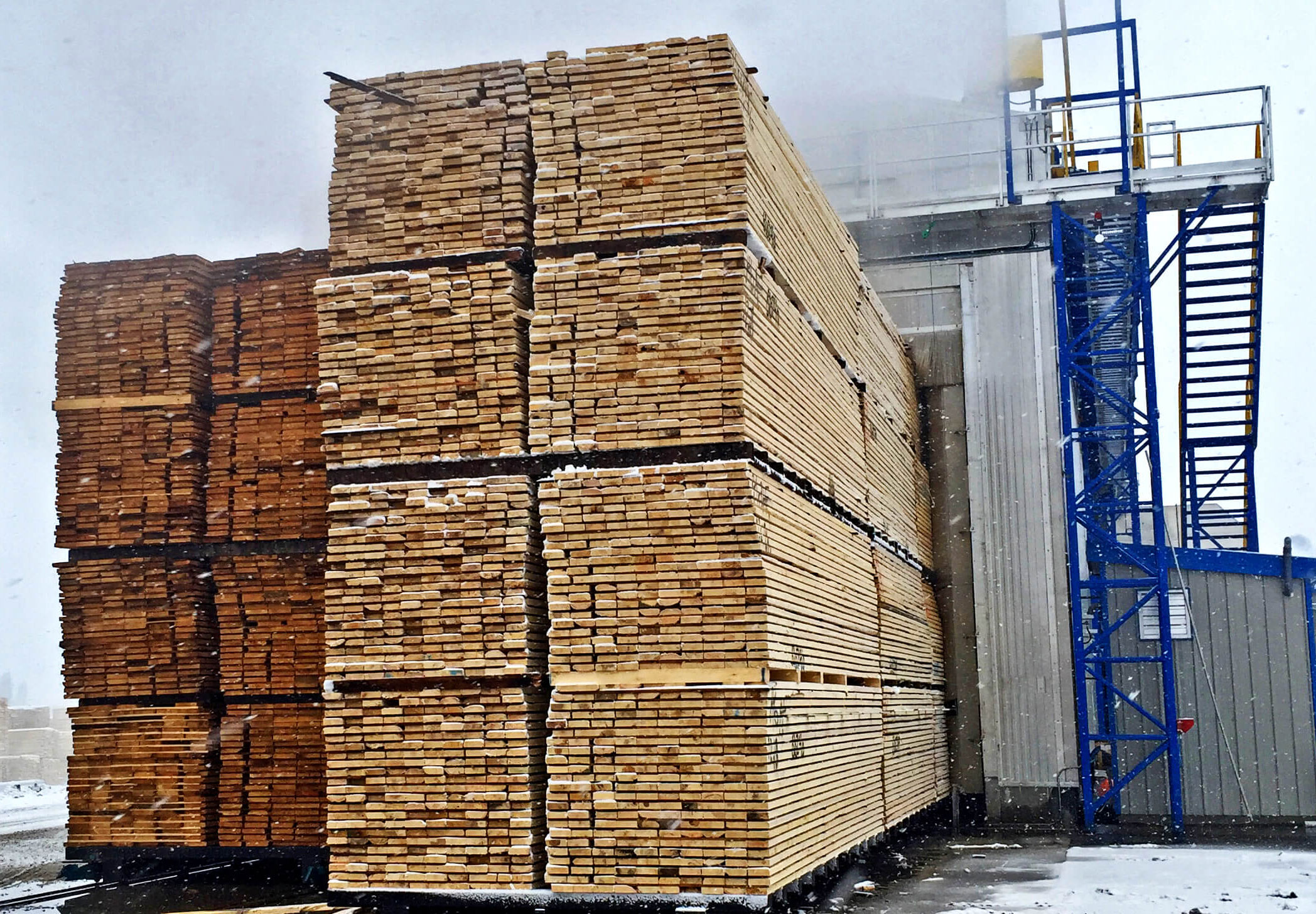
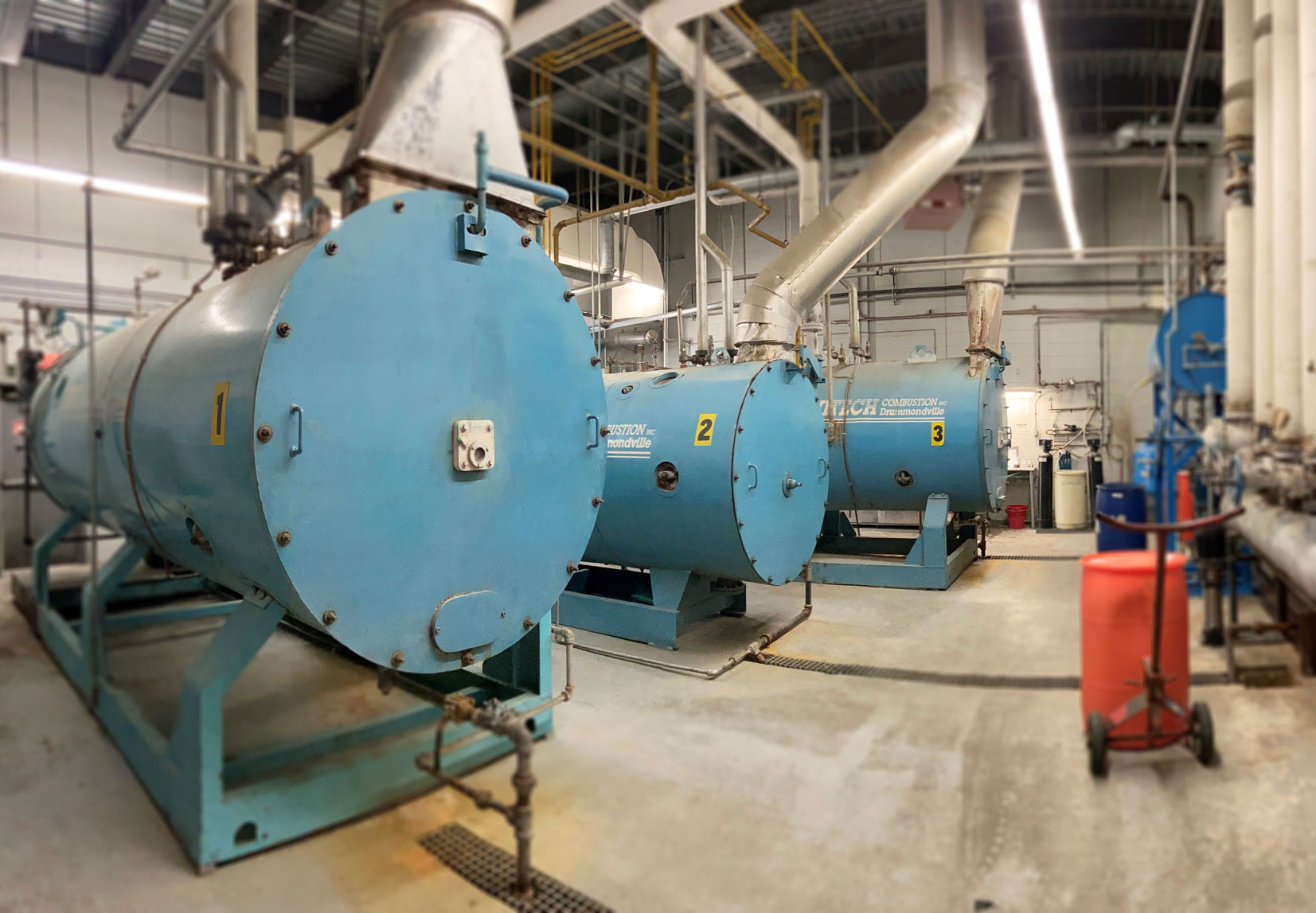
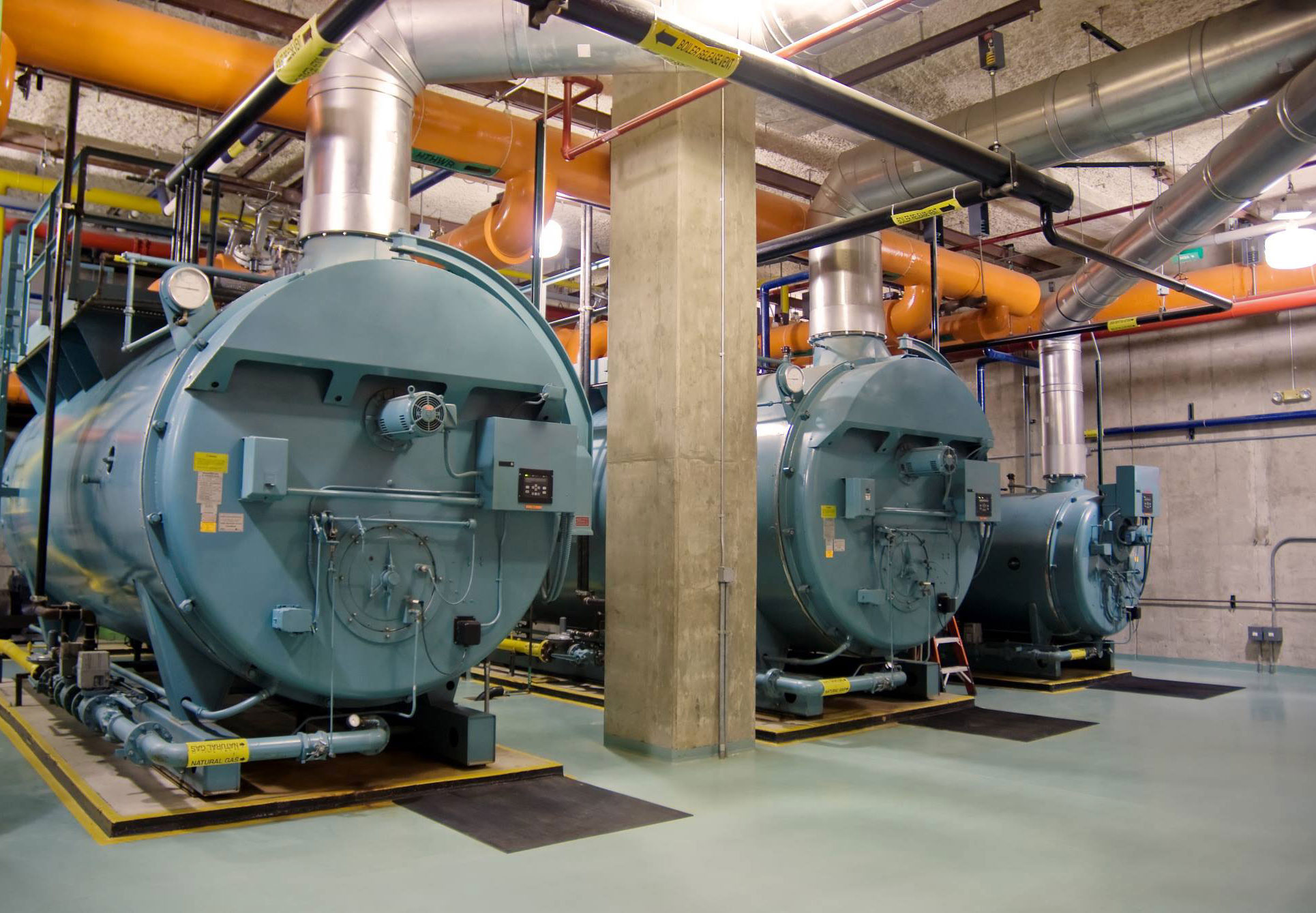
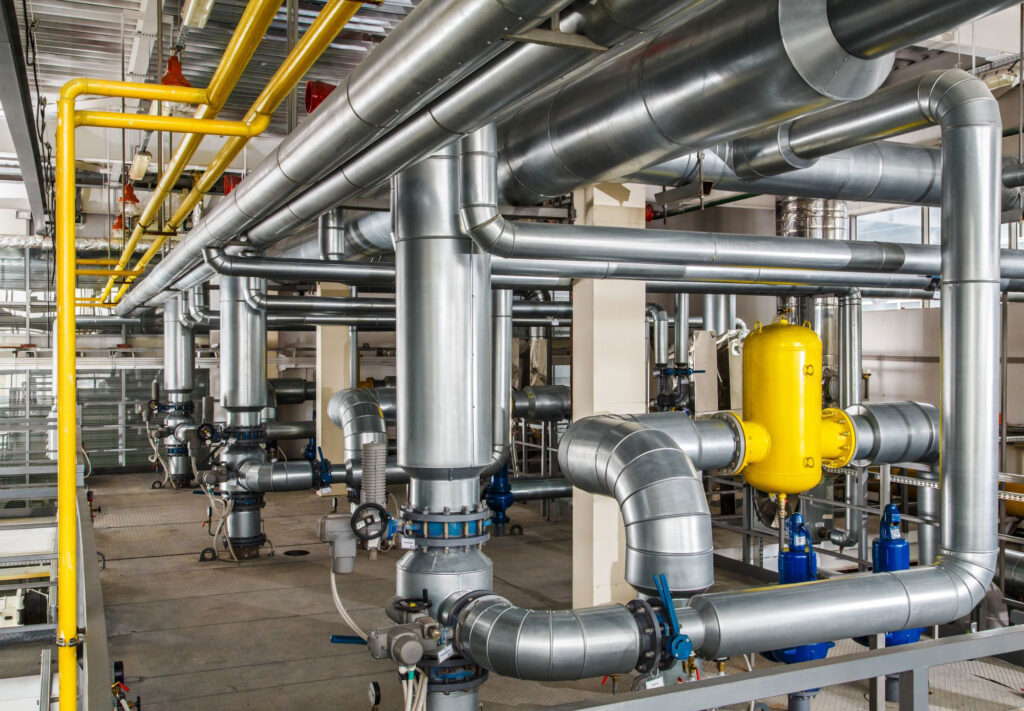
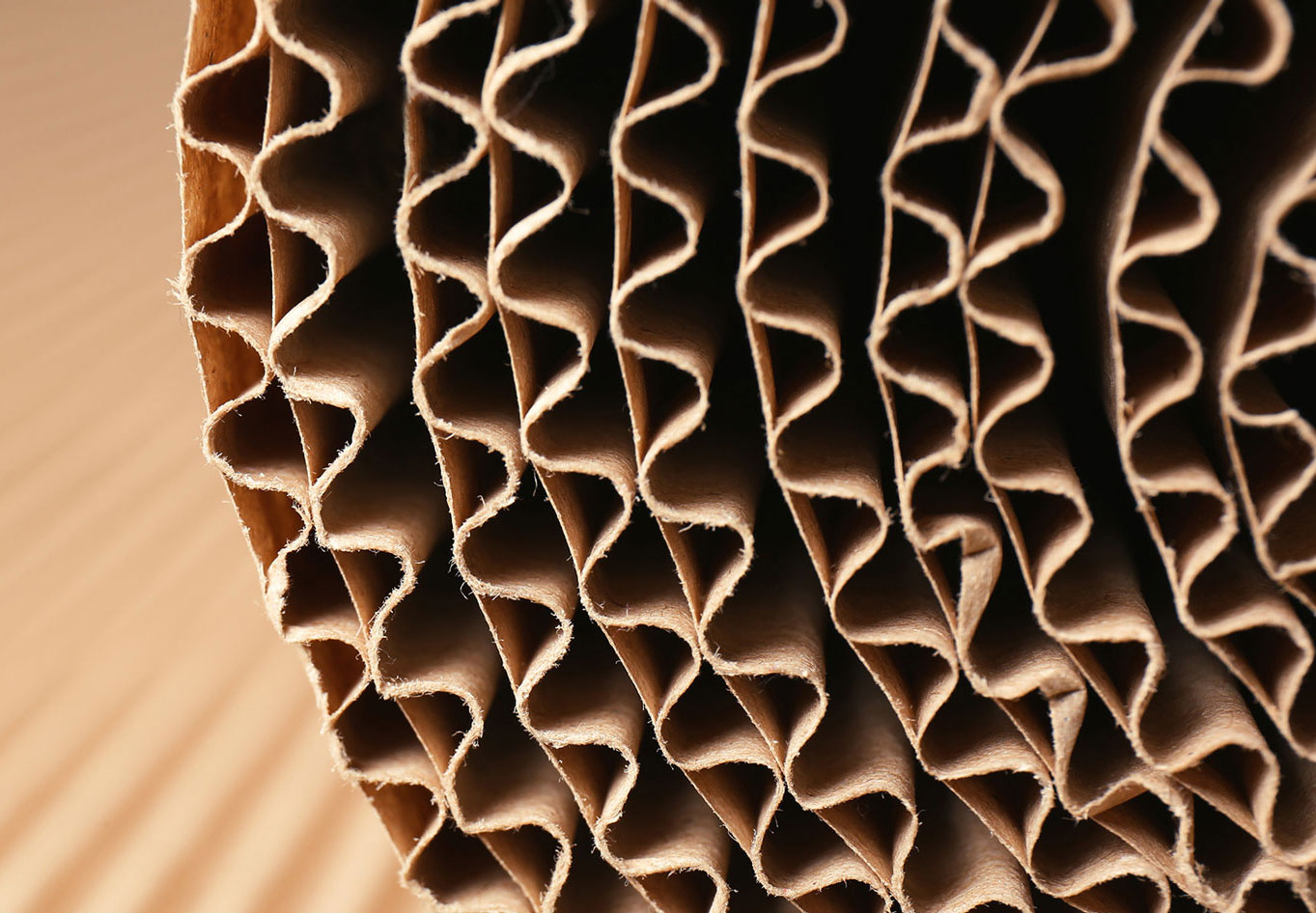
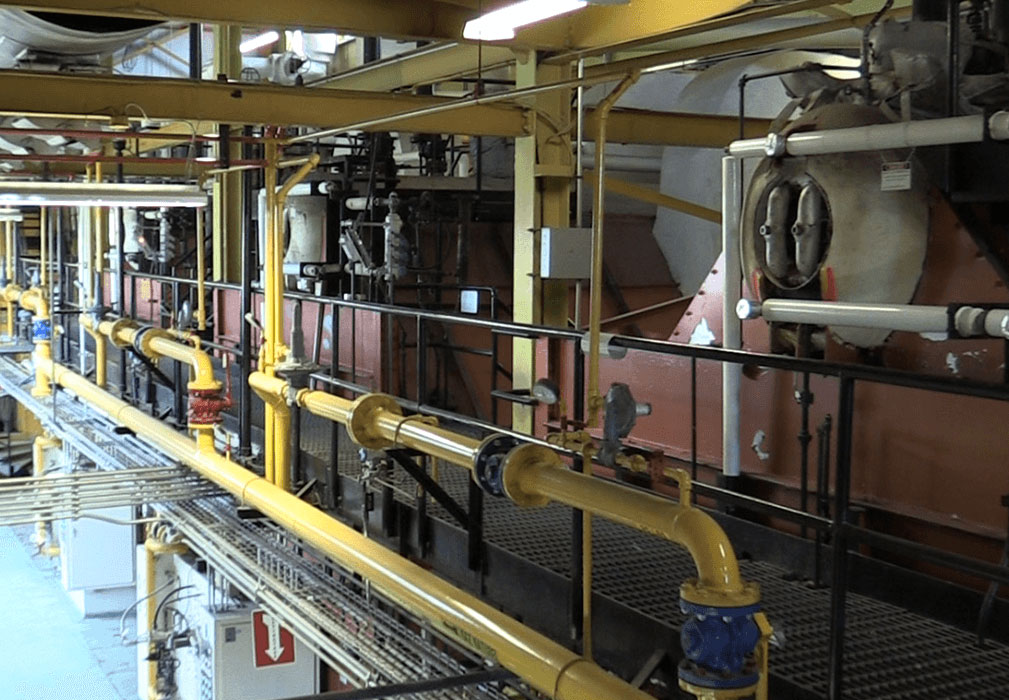
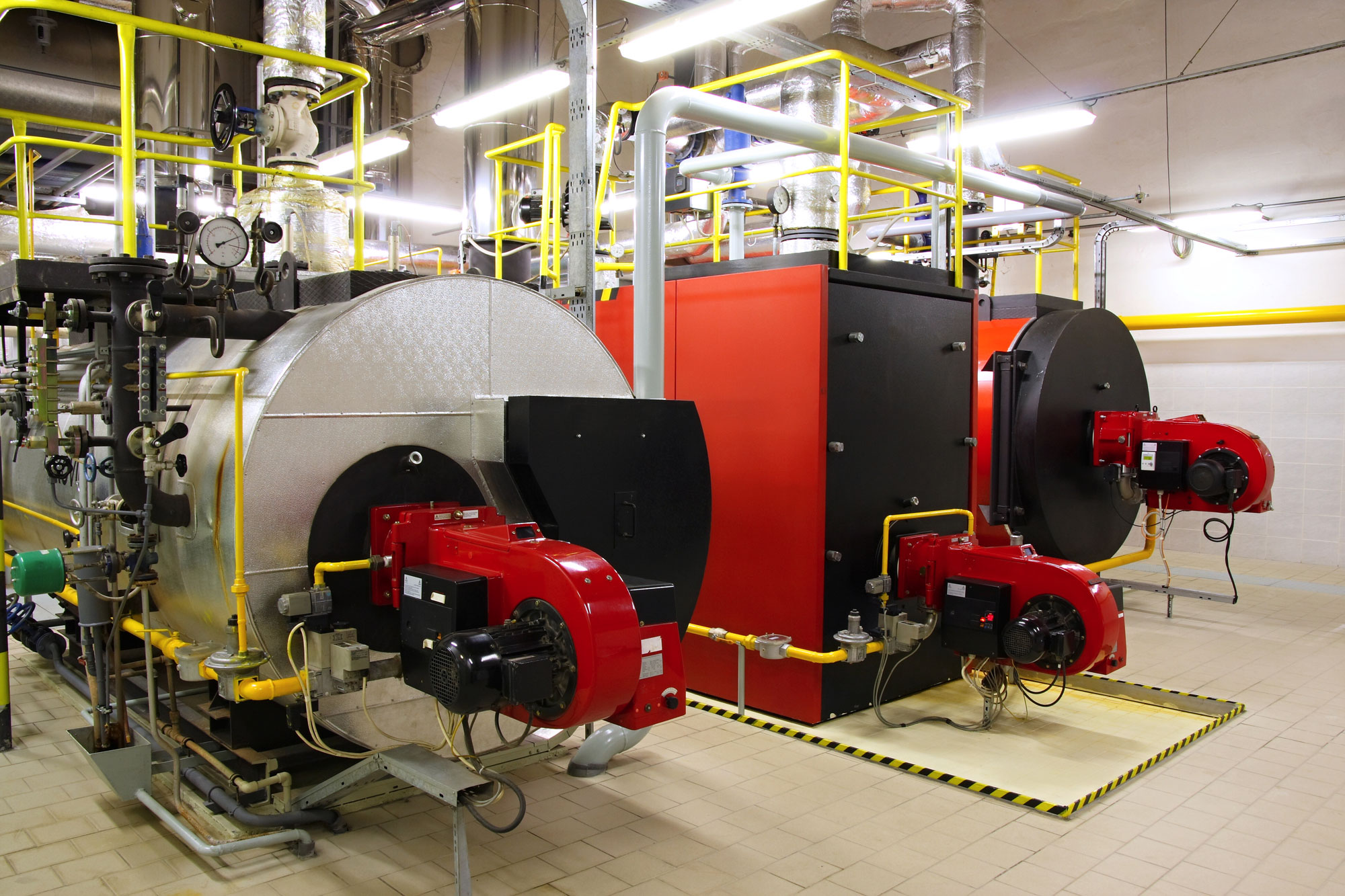
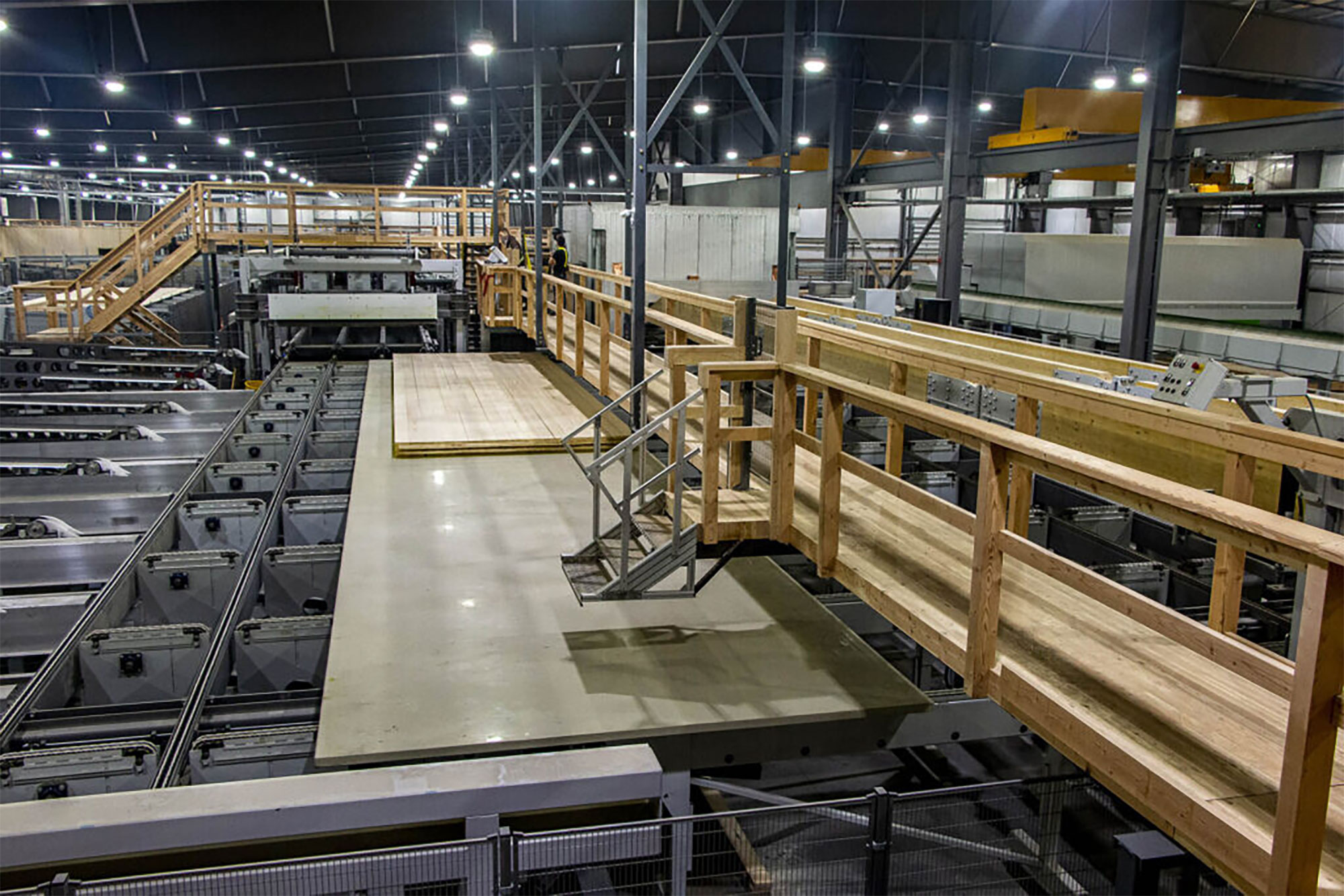
- What is the difference between film-forming agents and neutralizing amines?
Aquafilm V’s film-forming agents protect the entire steam network against corrosion by forming a protective film on the metal surfaces. This protection extends from the feedwater tank, to the boilers and condensate return lines.
However, neutralizing amines are not film-forming, and their role is to simply neutralize carbon dioxide (CO2) to prevent acid corrosion in the condensate; this function is limited and therefore does not protect the entire network. - What is the influence of the film-forming agents on heat exchange, considering that a film is formed on the surface of the metal?
The protective film is of molecular size and has no negative effect on the energy transfer in a boiler, but in fact, the heat transfer coefficients observed are higher for the tubes treated with film-forming agents than for those treated with conventional techniques.
How does Aquafilm V technology help to save energy compared to conventional applications?
Several factors impact the energy performance improvement of the steam system. Improved heat transfer and purge reduction significantly influence energy consumption.What is the anticipated purge reduction with Aquafilm V treatment?
If the purge is controlled to maintain the same level of conductivity in the boiler as with conventional treatment, the anticipated purge reduction typically ranges from 20% to 50% of the volume prior to the application of Aquafilm V.
Is the Aquafilm V treatment compatible with conventional treatment and must the system be purged before making the transition?
The technology is compatible with conventional treatment products. The sulfite concentration must not exceed 50 ppm at the time of Aquafilm V’s application.
Can the Aquafilm V treatment be used to clean a dirty boiler?
This is not recommended, as most scale deposits may be dislodged by treatment, but the released debris can cause localized fouling that may lead to overheating and tube breakage. Therefore, it is recommended to clean the boiler, especially water tube boilers, before applying the Aquafilm V treatment.
What dosing equipment is required, and can I use the existing injection system with the Aquafilm-V program?
Aquafilm V products must be injected with an electromagnetic diaphragm metering pump made of Teflon and EPDM with Teflon seals. This pump must be connected and controlled by a device to measure the flow of makeup water.